LENS MATERIALS
Lenses today are available in a wide variety of material and designs.
It’s our job to match the prescription and the patient’s visual needs
with the best lens choices. To do this we need to know the different
materials, their designs and be able to explain their features and
benefits to the patient.
Glass (Crown Glass)
For years glass was the number one choice for lens materials. With
the most precise and constant optics, glass is considered to offer the
most natural and comfortable vision. Untreated glass is not resistant to
breakage, therefore ANSI (American National Standards Institute)
standards state that all glass ophthalmic lenses must be either heat, or
chemically hardened to improve impact resistance. Many of the older
glass seg styles and tints are no longer available, or are only
available at a high cost. Some colors can be obtained by coating the
lens, although the cosmetics involved are questionable. Glass lenses are
spherical design only and considered to be old technology by most
dispensers.
Features and Benefits: Excellent optics and the best
scratch resistance of all materials. Remember, nothing is “scratch
proof”. Fused segments meaning there is no lip on top of segment like
all plastic materials have. Glass lenses take AR Coating excellently.
Negatives: Glass is the heaviest material available
as well as the lens “most likely to break”. Glass also pits and scars
when being used by welders. No aspheric designs available now, but they
are coming. Tints in Glass lenses are built into the material, this
includes glass photochromics. This will cause minus lenses to be darker
around the edge and plus lenses to be darker in the center. To avoid
this, use another lens material, or coat the lens for uniform density.
Flat top bifocals and trifocals in glass photochromics are a different
material from the rest of the lens and are clear, causing the bifocal
portion to be lighter in color than the rest of the lens. There is no UV
protection in clear glass lenses.
Plastic Hard Resin - CR-39
The
number one lens choice in today’s optical market according to the sales
numbers. Plastic’s excellent optics, comfortable abbe, lightweight, ease
of tinting and durability make it the most common choice among
dispensers. There are more lens styles and blank sizes available in
plastic today than any other lens material. Improved scratch resistant
coatings have helped sales and should always be recommended.
Features and Benefits: Plastic is roughly one half
the weight of a comparable glass lens. Plastic will accept tints easier
than any other material, it can be treated for UV, scratch coatings are
available, takes AR and almost any other lens treatment available.
Negatives: While standard plastic is the most common
lens sold today, it’s old technology, the equivalent of giving someone
an AM radio that wants a good sound system. About 30% thicker than
glass, plastic requires that scratch coatings and UV enhancements (at an
additional cost), rather than being built into the material like the
newer products. While available in aspheric design, the additional cost
is the same as going to an aspheric designed Mid to Hi Index lens.
Return to Top
Polycarbonate
Most impact resistant of all lens materials used today, polycarbonate
has been the best choice for safety eyewear, kid’s glasses and sports
eyewear. Polycarbonate has the added advantage of being a natural UV
filter, protecting to 380 nm UVA and all UVB. While it has one of the
higher indexes, it has a low specific gravity making it lighter in
weight than most other lenses.
The Optical Laboratories Association has a program called “Duty to
Warn” available to help educate your patient on polycarbonate and their
choices. Proper positioning (4-5mm below the center of pupil) on single
vision, good frame selection (No more than 5mm of decentration per eye,
preferably less) will help avoid problems. We recommend the addition of
multi-layer AR coatings to help provide the best vision for the patient
Features and Benefits: The safest, lightest and one
of the thinner materials available. New super tough scratch coatings can
make this the most scratch resistant material available for a small
added charge. Now available in aspheric designs that widen the viewing
area to about that of a Mid Index lens.
Negatives: Many polycarbonate lenses do not tint as
evenly, as dark, or as naturally as CR-39. Polycarbonate’s lower abbe
number can result in more chromatic aberration than some other lenses.
Proper fitting and aspheric design can correct this.
Return to Top
Hi Index Glass
The
word Index refers to the Index of Refraction of a given material.
Generally, the higher the index of refraction, the thinner the lens.
Crown glass has an index of 1.523 and is standard for glass lenses. Hi
Index Glass lenses come in 1.60, 1.70 and 1.80 and 1.90 indexes. Because
of their higher specific gravity, Hi Index glass lenses actually get
heavier as the index increases, however today’s smaller frames can
sometimes make this weight negligible.
Features and Benefits: Excellent optics and the best
scratch resistance of all materials. Nothing is “scratch proof”. Reduce
thickness as index increases. AR is more scratch resistant on all types
of Glass because of the harder surface.
Negatives: Weight increases as index increases.
While 1.60 can be hardened and will pass the “drop ball” test, 1.70,
1.80, and the new 1.90 indexes may not meet ANSI standards for impact
resistance and will probably require a waiver from the patient and
doctor. Increased chromatic aberration basically demands an AR coating.
No aspherics available at last notice.
Return to Top
Hi Index Plastic
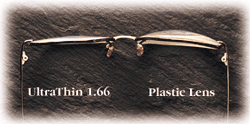
The term Index refers to the Index of Refraction of a given material.
The higher the index of refraction, the thinner the lens. Regular
plastic lenses have an index of refraction of 1.498. Hi Index plastics
range from an index of 1.54, up to the
new 1.74. Unlike glass, that gets heavier as the index gets higher,
plastic Hi Index lenses generally offer lighter weight than regular
plastic lenses. TIP: We recommend AR coating on both glass and plastic
Hi Index lenses as the higher indexes also mean lower abbe values. If
you have a Hi Index non adapt, try coating the lenses, or moving them to
a Mid Index.
Look at Hi Index as 4 separate levels, Mid Index 1.54 to about 1.58 -
Hi Index 1.60 - Hyper Index 1.66 and the new Hyper Index 1.74. It’s best
to specify the index and whether or not you want an aspheric design,
unless you care to trust your lab with picking the “best choice” and
then you need to let them know that’s the case. While polycarbonate is
technically a Hi Index plastic material, poly is almost always treated
separately from other lens types.
Return to Top
Mid Index 1.53 (NEW)
This mid index lens is a brand new monomer that is set to challenge
polycarbonate as “the lens for safety purposes. With its higher abbe,
better scratch resistance, ease of tinting and aspheric design, we
finally have an alternative to polycarbonate for safety and children’s
eyewear.
Mid Index 1.54 to about 1.58
This mid index range makes a noticeable improvement over standard
plastic, but is most effective in certain products that include aspheric
design at no additional charge. Check with your lab on their preference
here. The abbe value on this range is in the “comfort zone” that does
not require an AR coating, although AR is still and always recommended
for best vision.
Hi Index 1.60
This is the index most commonly associated with Hi Index, but like
the mid-indexes, is most effective in certain products that include
aspheric design at no additional charge. The abbe value of most 1.60
would suggest AR to help with chromatic aberration. Some 1.60 products
include aspheric design at no additional charge. Check with your lab on
their preference here.
Return to Top
Hyper Index 1.66
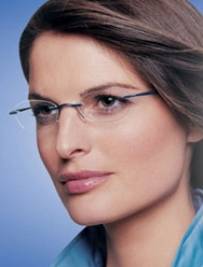
There are several manufacturers of the 1.66, 1.67 index lenses. All
of the lenses in this index are aspheric, with some of them also having
an “atoric” design.
Features and Benefits: All Hi Index lenses offer
built-in UV and scratch resistance. Aspheric is built-in in some lenses
and must be specified in others. Hi Index lenses provide thinner,
lighter lenses than the older regular plastic lenses.
Negatives: In the upper indexes a small number of
patients may experience chromatic aberration and report seeing a “color
fringe” in peripheral vision. This can usually be avoided with the
choice of smaller frames, proper positioning and the addition of an AR
coating
Return to Top
Polarized Lenses
Virtually all prescription polarizing lenses, glass, plastic, and
polycarbonate protect the eye from damage caused by long term exposure
to ultraviolet light. This is a big benefit, since the same surfaces
that reflect light in a polarized manner also reflect a high amount of
UV light. Listed below are approximate percentages of UV absorbing
polarized lenses.
More Advantages of Polarized Lenses:
Driving fatigue is reduced--Much of the light reflected from large
pavement is polarized, so people who do a lot of daytime driving will
benefit from polarizing lenses.
Fishing and other outdoor water activities enhanced--Light reflected
from the surface of the water prevent the viewer from seeing below the
surface. Polarized lenses not only eliminate this glare, but enables the
wearer to see below the surface as well. Also, sand at the beach is a
source of this same glare.
Snow is very reflective--People who are out working or driving in the
snow will see the benefit from using polarized lenses.
Everyone can benefit from polarized lenses--So many cases of glare occur
during the day, (bumpers on cars, windows on buildings) a good
demonstration can show how everyone can benefit. When glare disappears
color returns.
Did You Know...?
In sunlight there are two bands of radiation that can affect your eyes:
UVA can cause sun tanning, wrinkles, and sagging skin. It may also be
harmful to the cornea and the retina of the eyes. UVB is higher-energy
radiation.... and more dangerous. This band of radiation, also known as
the sunburn rays, can cause photokeratitis (snow blindness is an example
of photokeratitis).
Return to Top |